Acorn the curved concrete floor, reusable and removable
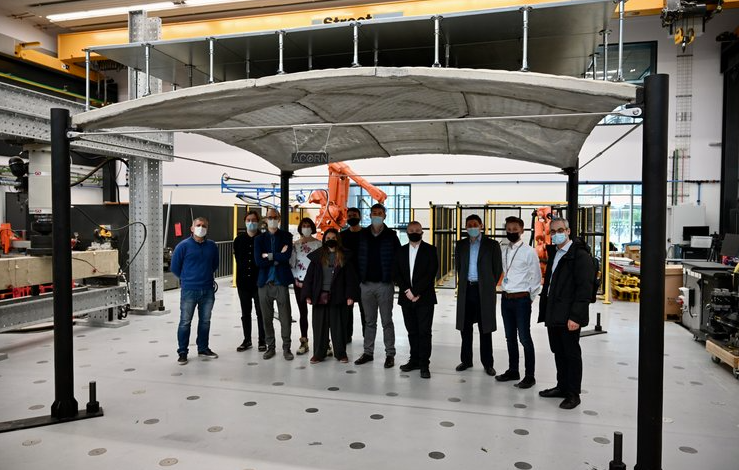
The ACORN project developed a prototype of a factory-sprayed curved floor and a non-prismatic beam
(Sustainabilityenvironment.com) – With the aim of making the construction industry more efficient, sustainable and circular, researchers at the University of Bath, Cambridge and Dundee have launched the ACORN project.
Acronym of Automating Concrete Construction, the project takes advantage of digitalization and automation, to significantly improve the construction process, acting on one of the most “impacting” environmental, concrete.
The research carried out by the ACORN project is manifold, from the prefabricated, transportable and reusable vaulted floor to the non prismatic beam that follows the distribution of the bending moment and is formed with flexible formwork.
Goodbye to prismatic formwork
“Creating beams, columns and slabs that have the right shape to perform their work well, rather than the right shape to be easily formed,” comments Professor Paul Shepher of the Department of Civil Architecture and Engineering at the University of Bath, and one of the proponents of the project.
Almost half of the concrete currently used in building construction is superfluous. It’s only present because, for centuries, we have been accustomed to using planar formwork in which to pour the material. However, these forms are not always the most efficient from a structural point of view, and among other things, they represent the main factor of the embedded emissions of a building.
The slabs to which we are accustomed consist of flat concrete slabs subjected mainly to bending loads. Since the concrete does not have particular resistance to bending induced by tension, the floor slab must be helped with steel reinforcements.
The approach of the ACORN project does exactly the opposite: it puts the concrete in a position to resist the force to which it best responds, the compression. The material is placed only where it is strictly necessary to use it in compression, in this way you use only a quarter of the concrete normally used to support the same load.
The vaulted prefabricated floor
The optimal shape that the researchers have identified is a vaulted floor, very thin and curved, which would be impossible to obtain with traditional formwork. The concrete is sprayed in a controlled environment, outside the site where it will be installed. With the help of software and robotics, the molds consist of vertical pins carefully positioned by digital instrumentation, which support a flexible formwork, adaptable to a curved surface.
At the same time, software identifies the optimal shape suitable for the building that is being built, dividing if necessary the floor into several elements. Once sprayed and transported on site, the floor elements are assembled with special joints. All obviously always subjected to the constant monitoring of the software.
Circular economy and reduced time
A further interesting aspect is that the joints are designed to be reversible. This means that at the end of the life of the building, the floor and its components can be transported elsewhere, with a view to a perfect circular economy.
The test version of ACORN’s first floor used 75% less concrete than the equivalent flat slab. CO2 emissions have been reduced by 40% and with them construction times and especially costs.
ACORN has received funding from UK Research and Innovation under the ISCF Transforming Construction program.